Le filtre presse à plateaux : un procédé ultra performant
Le filtre presse à plateaux est le procédé de filtration et de déshydratation mécanique le plus performant qui permet d’atteindre des siccités de 30 à 80%. Il est utilisé pour la déshydratation des boues provenant d’effluents industriels et urbains mais aussi pour de la filtration au cœur de procédés dans la chimie, la pharmacie, l’agro-alimentaire, la céramique, les mines et les carrières.
Composition d’un filtre presse
Un filtre presse est composé d’une succession de plateaux recouverts de toiles filtrantes, serrés au moyen d’un ou deux vérins hydrauliques entre un sommier fixe et un sommier mobile. L’étanchéité au niveau des plans de joint est assurée par un serrage à une pression de 200 à 300 bars. Faure Equipements propose des filtres presses équipés de plateaux de 250 x 250 mm jusqu’à 2 000 x 2 000 mm pour des volumes variant de 2 à 20 000 litres.
Le produit à filtrer est introduit par l’intermédiaire d’une pompe jusqu’à la pression nécessaire (généralement 7 à 15 bars). Sous cette pression le liquide passe à travers la toile qui retient les particules solides. Ce filtrat est collecté soit au niveau de chaque plateau soit en bout de filtre. L’accumulation de matière entre les plateaux induit une perte de charge qui est compensée par la pompe d’alimentation. Celle-ci doit alors réguler son débit en fonction de la pression dans le filtre presse. A noter que certains produits nécessitent une étape de conditionnement préalable au moment de la filtration par l’ajout de réactifs qui permettent ainsi leur filtration. Cette préparation fait partie intégrante de notre savoir et de nos prestations au travers de nos unités de déshydratation clé en mains et des essais éventuellement nécessaires.

Un filtre presse peut être équipé de plateaux à membrane. Cette membrane déformable sous l’action d’air ou d’eau sous pression permet un compactage des gâteaux à la suite de la phase de filtration. Dans ce cas, la pression de filtration est le plus souvent de 8 bars et c’est le compactage qui assure la pressurisation des gâteaux à 15 bars. L’avantage de ce type de plateaux est d’augmenter les performances de déshydratation, d’améliorer la productivité et de favoriser la chute des gâteaux. Cela permet également d’effectuer du lavage et du soufflage de gâteau, si nécessaire, dans des conditions optimales.
PHASE DE DÉBÂTISSAGE
En fin de cycle, les gâteaux formés à l’intérieur des chambres du filtre presse sont évacués en écartant progressivement l’ensemble des plateaux. Cette opération de débâtissage peut être manuelle, mécanisée ou automatisée sur la dernière génération de filtres presses grâce au robot full auto.
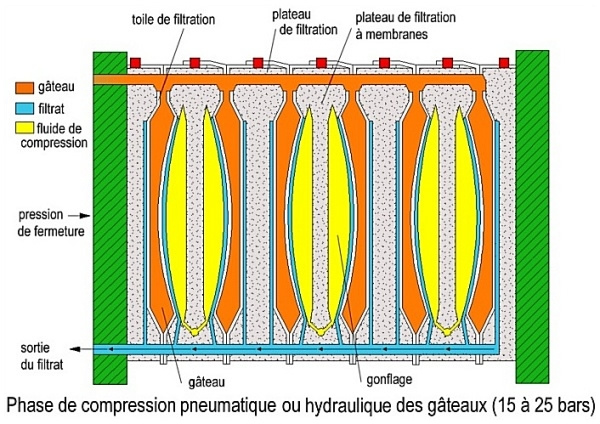