The plate filter press: a high-performance process
The plate filter press is the most efficient mechanical filtration and dewatering process that can reach a dryness level of 30 to 80%. It is used for dewatering sludge from industrial and urban wastewater, but also for filtering at the core of chemical, pharmaceutical, food processing, ceramic, mining and quarrying processes.
Components of a filter press
A filter press is formed by a succession of plates covered with filter cloths, clamped by means of one or two hydraulic cylinders between a static and a movable frame. The sealing at the joint level is ensured by tightening at a pressure of 200 to 300 bar. Faure Equipements offers filter presses equipped with 250 x 250 mm to 2,000 x 2,000 mm plates for volumes ranging from 2 to 20,000 liters.
The substance that requires filtering is fed through a pump to the required pressure (usually 7 to 15 bar). Under this pressure the liquid flows through the cloth which retains any solid particles. This filtrate is collected either at each plate or at the end of the filter. The deposit of material between the plates induces a pressure drop which is compensated by the feed pump. Then this pump must regulate its flow rate according to the amount of pressure in the filter press. It should be noted that some products require a conditioning step prior to filtration by adding reagents that allow their filtration. This process is an integral part of our knowledge and the services we offer through our turnkey dehydration units and after any required testing is done.
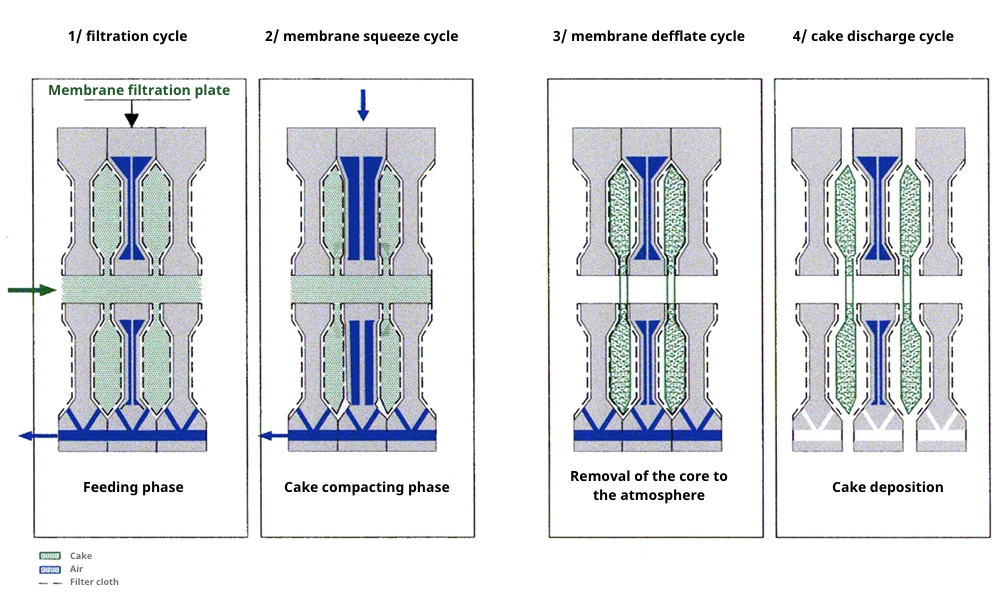
A filter press may be equipped with membrane plates. This membrane, which can be distorted by pressurized air or water, allows cake compacting following the filtration phase. In this case, the filtration pressure is usually 8 bar and the compaction ensures cake pressurization at 15 bar. The main benefit of this kind of plate is to increase dehydration performances, to improve productivity and to facilitate cake fall. It also allows to perform cake washing and blowing, if necessary, under optimal conditions.
At the end of the cycle, the cakes formed inside the filter press chambers are removed by progressively pushing aside all the plates. This process can be done manually, mechanically or automatically on the latest generation of filter presses using the full auto robot.
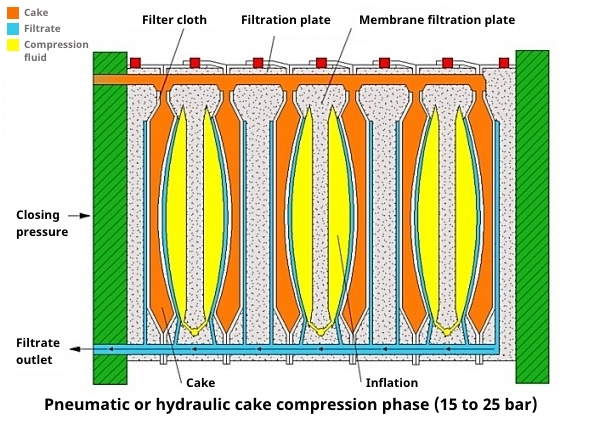